Обогнать рынок: 5 шагов по повышению производительности труда на предприятиях
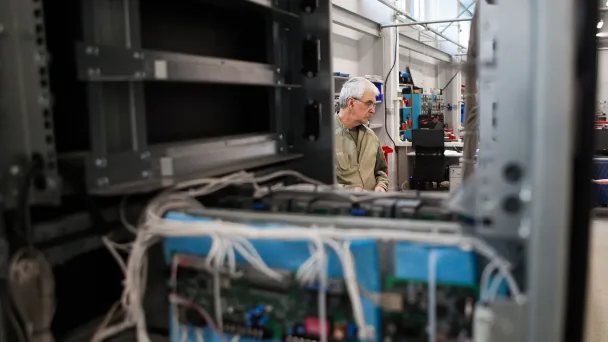
Национальный проект «Производительность труда» включает в себя целый ряд мер поддержки предприятий, но в первую очередь быстрый и устойчивый рост обеспечивает внедрение принципов и инструментов бережливого производства. Сделать это столичным предприятиям помогает команда экспертов Регионального центра компетенций (РЦК), созданного на базе Агентства стратегического развития Москвы.
В национальном проекте могут принять участие компании из пяти приоритетных отраслей: транспорт, торговля, строительство, обрабатывающая промышленность и сельское хозяйство. За последние пять лет число таких предприятий выросло вдвое, а их совокупный оборот составил 80,8% от общего оборота крупных и средних предприятий Москвы (42,6 трлн рублей). Рабочими местами они обеспечивают более 1,25 млн человек.
«Наша задача в текущей ситуации — не только помочь ключевым отраслям сохранить заданные темпы развития, но и ускорить адаптацию к новым экономическим условиям. Именно для этого Агентство стратегического развития Москвы работает с компаниями в индивидуальном порядке, находя и устраняя все виды производственных проблем, которые мешают эффективному росту. Но это не просто разовое мероприятие — инструменты бережливого производства внедряются в культуру компании, чтобы в дальнейшем любые изменения уже являлись для компании не вызовом, а точкой роста. Национальный проект стартовал в этом году, но мы уже видим первые результаты. За это время реализацию программ по улучшению производственных процессов начали 24 предприятия. По промежуточным результатам в среднем на таких производствах выработка увеличилась почти на треть, а время протекания процессов и незавершенное производство уменьшились как минимум вдвое. Всего на данный момент в агентство подано более 200 заявок от столичных предприятий, из которых 95 прошли очные отборы», — говорит Мария Багреева, министр Правительства Москвы, руководитель Департамента экономической политики и развития города.
Ряд компаний уже получили первые результаты и поделились с нами своим опытом. Для вашего удобства мы выделили из их рассказов пять важных шагов по повышению производительности.
Шаг 1. Обозначить цели
Обозначить цель совсем несложно, а вот составить план по ее реализации — очень. Для того чтобы получать желаемые результаты, нужно уметь видеть перспективы, находить слабые места производства и более конкретно ставить задачи по их устранению. В такие моменты порой очевидна становится необходимость внешнего эксперта — внутри компании всегда сложно увидеть неоптимальные моменты в привычных процессах. Взгляд со стороны способствует качественному анализу каждого из производственных процессов. Многие столичные компании решили участвовать в нацпроекте «Производительность труда» именно по этой причине — они искали наиболее оптимальный путь к своей цели.
Например, производитель светодиодных осветительных приборов «ЛЕД-Эффект» хотел максимально использовать открывающиеся на рынке возможности. За 12 лет работы ассортимент компании вырос с одного до более 6000 продуктов. Самый активный рост пришелся на последние три года. Менеджмент начал заниматься оптимизацией бизнес-процессов, а в 2022 году пришлось резко ускориться. «С уходом иностранных компаний, поставлявших дизайнерское освещение на российский рынок, открылись новые возможности, — говорит совладелец компании «ЛЕД-Эффект» Мария Кошелева. — Но без повышения эффективности всех процессов и всех сотрудников у нас может не хватить ресурсов на разработку и запуск инновационных продуктов. Базовые процессы должны работать как часы. Поэтому для нас участие в нацпроекте — важный шаг вперед».
Строительно-производственная компания «БиоПласт» уже 15 лет производит на трех своих заводах трубопроводы, очистные сооружения, емкости, насосные станции из современного композитного материала и многое другое. К нацпроекту она присоединилась, чтобы максимально соответствовать требованиям крупных заказчиков, среди которых такие компании, как НЛМК, «Северсталь», «Роснефть», «Сбербанк девелопмент» и другие. «В последнее время мы часто сталкиваемся со срочными заказами, такими, например, как поставка более сотни изделий для строительства скоростной автомобильной дороги М12 Москва — Казань — Екатеринбург всего за 45 рабочих дней. Или со сложными заказами, сроки исполнения которых из-за множества согласований и изменений заметно уменьшаются. Компании важно иметь отлаженные, эффективно работающие производственные процессы, чтобы исполнять контракты в согласованное с заказчиками время. Вся команда — от собственника до линейных руководителей — хочет выйти на новый уровень качества, повышение производительности и снижение себестоимости», — рассказывает исполнительный директор «БиоПласта» Владислав Алимов.
А ГК «Москабельмет», производящая кабельно-проводниковую продукцию, стала участницей нацпроекта, решая в связи с ростом заказов дилемму — увеличить парк станков или повысить производительность. «Когда замылен глаз и кажется, что вы достигли определенной высоты, взгляд со стороны позволяет увидеть внутренний потенциал», — говорит генеральный директор ГК «Москабельмет» Павел Моряков.
Шаг 2. Вовлечь каждого
Для того чтобы изменения прижились на предприятии, все сотрудники на своем уровне должны понимать их необходимость. Этому способствует как выстраивание грамотной коммуникации в компании, так и обучающие программы по методике бережливого производства.
Информированность о том, что происходит на предприятии, оказалась очень важна для рядовых сотрудников, отмечает Владислав Алимов из «БиоПласта»: «Они прямо говорят, что знания об изменениях и новых задачах компании дают им чувство сопричастности и мотивируют работать лучше».
На «Фабрике Вентиляции ГалВент» не раз приглашали высокооплачиваемых консультантов по оптимизации работы топ-менеджеров, но внедрить новый подход системно не удавалось. В рамках нацпроекта обучение прошли руководители всех уровней, включая бригадиров участков и звеньевых, а также несколько рабочих. «Мы поняли: из-под палки ничего не получится. Нужно объяснить людям, зачем им это необходимо», — говорит генеральный директор «Фабрики Вентиляции ГалВент» Кирилл Прахов.
Так, в рамках обучения тренеры разделили участников на две команды и предложили на скорость выполнить задачу по быстрой переналадке оборудования. Одна команда справилась за шесть минут, вторая — за восемь. Когда тренер предложил использовать инструмент бережливого производства SMED, который минимизирует потери при переналадке оборудования, команды выполнили схожую задачу в разы быстрее. «Всех заинтересовала такая эффективность, поскольку персонал работает сдельно», — объясняет Кирилл Прахов.
После тренинга воодушевленные участники диагностировали 73 проблемы на наиболее трудоемком производственном участке — по выпуску прямоугольных фасонных изделий. Например, при сборке одного воздуховода у рабочего уходило только две минуты на промазку герметиком швов. Тогда сами сотрудники продумали, как организовать рабочее место по системе 5С (удобно расположить инструменты и герметик, повернуть деталь и изменить положение рук), и время на одну промазку снизилось до 20 секунд.
Предложения по улучшению появились после тренинга и на других предприятиях, где участники поняли связь между организацией рабочего места и скоростью выполнения задач. К примеру, на «Парус электро» рабочие снизили время на опрессовку детали с 15 минут до четырех. Оказалось, что для этого достаточно было удобно разместить инструменты, рассортировать комплектующие по ящикам разного цвета, а главное — расположить под рукой механическое оборудование (пневмопистолет). По словам технического директора «Парус электро» Максима Солонинкина, с мая по начало августа сотрудники «Парус электро» внесли 14 предложений, и все они были внедрены в цеха. Благодаря этому совокупное время производства одной электрозарядной станции снизилось с 60 до 46 часов.
Однако не все так просто. Именно поэтому важно, чтобы и сотрудники, и руководство не забывали цели внедрения. Максим Солонинкин приводит конкретную ситуацию. Переорганизация рабочих мест заняла часть рабочего времени, что вызвало недовольство у менеджеров. «Мне было сложно объяснить руководству, почему мы проводим сортировку комплектующих по 5С вместо сборки, — говорит он. — Но все согласились дождаться первых результатов». К концу мая время производства электрозарядных станций сократилось на 22%, а количество незавершенного производства — на 44%. Топ-менеджеры «Парус электро» вошли в рабочую группу по повышению производительности и теперь с интересом рассматривают предложения сотрудников.
Шаг 3. Внедрить инструменты бережливого производства
Перестройка процессов возможна лишь при системном подходе. За первые полгода участия в нацпроекте компания проходит оценку производства, занимается совместно с экспертами РЦК постановкой задач и работой над пилотной линией — одним конкретным участком предприятия. На разных уровнях происходит обучение инструментам бережливого производства, среди которых декомпозиция целей, производственный анализ, картирование процессов и многое другое.
Часть компаний специально выбирают в качестве опытного участка трудоемкое производство, требующее взаимодействия с другими участками предприятия. А другие — линию выпуска ключевого продукта, который занимает самую большую долю в выручке предприятия, — ведь эффект от сокращения сроков производства станет в данном случае очевиден всем. Именно поэтому, например, компания «ЛЕД-Эффект» выбрала для пилота производство уличных светодиодных светильников «Кедр», эта серия приносит 30% прибыли предприятия, а в ее производстве участвуют почти все линии сборки.
Практически на каждом предприятии уже в начале внедрения практик бережливого производства случились неожиданные открытия. Например, топ-менеджеры компании «БиоПласт» совместно с экспертами РЦК выявили избыточные перемещения заготовок и персонала, так называемую избыточную логистику, которая приводила к увеличению времени производства продукции. В итоге сотрудники предприятия разработали новый план размещения производственных участков с оптимальным перемещением по цеху.
На другом предприятии «Арисмо инжиниринг» оценка эффективности выполнения работ показала, что скорость работы специалистов одной квалификации может различаться в 3,7 раза. Для сотрудников было не просто проведено обучение, но и изменена система оплаты труда так, чтобы увеличить мотивацию работать быстро и качественно, — теперь они могут заработать в 1,5 раза больше, но благодаря увеличению общей выработки компания совсем не потеряла доход.
«Уже на первом этапе программы выработка в смену в сборочном цеху увеличилась на 52%, — говорит гендиректор «Арисмо инжиниринга» Сергей Овчинников. — Это произошло благодаря комплексным изменениям по принципам бережливого производства, среди которых перепланировка сборочного цеха, организация рабочих мест по системе 5С, внедрение адресного хранения на складе».
Главный результат этого этапа нацпроекта, помимо повышения производительности на выбранном пилотном участке, — принципиально новое восприятие производства как сложной многоуровневой системы, эффективность которой зависит от множества факторов, которым возможно раньше руководители могли не уделять должного внимания.
Шаг 4. Масштабировать новые практики
После шести месяцев реализации проекта на предприятии обучением сотрудников компании обычно занимаются уже свои сертифицированные тренеры, а эксперты РЦК скорее контролируют и корректируют процессы. Масштабирование новых практик с пилотной линии на все производство занимает следующие два с половиной года участия в нацпроекте.
Но начинается этот этап обычно раньше. Например, на «Фабрике Вентиляции ГалВент» пилотный проект идет на участке по выпуску прямоугольных фасонных изделий. Как только он стартовал, стало очевидно, что каждую смену работник тратит до полутора часов на поиск нужных заготовок (они мало отличимы внешне). Для решения этой проблемы внедрили систему адресного хранения с QR-кодированием, и время поиска сократилось до двух минут. Точно такая же ситуация обнаружилась и на смежном участке, на котором инструменты бережливого производства еще не внедрялись, однако практику с кодами применили сразу же.
Все участники нацпроекта в столице отмечают, что внедрение новых практик на других участках идет быстрее. Так, сотрудники компании «Парус электро» стараются сейчас самостоятельно внедрить бережливое производство на своем заключительном производственном этапе — в лаборатории, которая тестирует продукцию. «Сейчас все идет хорошо и приятно: рабочая группа заинтересована в процессе, сотрудники других подразделений спрашивают, когда дойдет очередь до них, — рассказывает Максим Солонинкин. — А главное, у людей остается больше времени на выполнение ключевых задач. К примеру, раньше из-за отсутствия налаженных информационных потоков и обратной связи технолог был вынужден тратить больше рабочего времени на ручное управление производством, теперь он, наконец, погружен в оптимизацию серийных продуктов».
Шаг 5. Продолжать улучшения
К окончанию нацпроекта производственная культура компании полностью перестраивается: стремление к оптимизации становится движущей силой постоянных улучшений. «Участие в проекте уже стало хорошей рекламой для бизнеса: приезжая на производство, клиенты видят, как предприятие развивается, и гораздо охотнее заключают контракты», — отмечает Максим Солонинкин из «Парус электро».
Компании, успешно справившиеся с первыми этапами, в рамках нацпроекта могут получить субсидии для развития. У части столичных участников уже появились идеи. Например, в «Парус электро» из-за прекращения поставок некоторых комплектующих из других стран задумались о запуске собственного цеха полиэтилен-пластмассы. Для его оснащения нужен дорогой станок, без субсидии предприятию покупка непосильна.
У некоторых компаний задачи еще амбициознее: «ЛЕД-Эффект» планирует стать лидером по производству энергоэффективного светодиодного освещения в России. «Мир быстро меняется, и мы должны двигаться еще быстрее, чтобы стать компанией номер один на рынке, — говорит Мария Кошелева. — Активное вовлечение сотрудников компании в процесс бережливого производства как нельзя лучше соответствует нашей миссии, ведь мы создаем комфортный свет с заботой о клиентах, партнерах и планете. Благодаря нацпроекту мы вкладываемся в развитие персонала и в комфортную среду. Уверена, что все вместе это дает кратный эффект для развития компании и нашей инновационной продукции».
При этом все столичные участники нацпроекта убеждены, что повышение производительности их компаний полезно и для экономики в целом, так что стимулов для непрерывного процесса улучшений компаниям точно хватит!