Белыми нитками: Смогут ли композиты поменять технологический уклад?
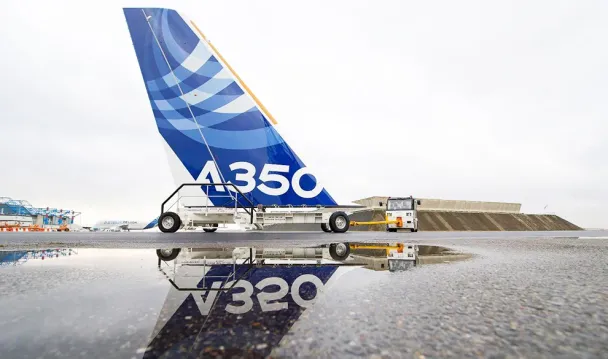
Каменный, железный, золотой — века. С тех пор как инженерная мысль научилась сочетать в одном изделии свойства двух или нескольких разных материалов, например, дерева и смолы, угля, стекла или пластика, технический прогресс начал ускоряться. Принято считать, что первыми композитные материалы стали использовать египтяне. В древнем мире шпон саркофагов и ткани, в которые оборачивали мумии, пропитывали древесными смолами.
В начале Средневековья монгольские войны научились изготавливать луки из сухожилий волов, рогов, бамбуковых стеблей, шелка, пропитывая их смолами сосны, воины умудрялись добиваться высокой прочности, которая уступает лишь 20% современным аналогам.
Около полувека назад расклад в сфере высоких технологий поменяли пластики — стеклопластики и углепластики стали активно использоваться в небе и космосе. В семидесятых годах советские технологи в обнинском ОНПП «Технология» создали первые композитные изделия для межпланетной космической станции «Венера». Новый материал позволял выдерживать перепад температур в сотни градусов по цельсию и в конечном счете успешно совершить спутнику путешествие в 100 млн километров, с далекой планеты успешно передали фотоснимки.
Прочнее стали
Самый популярный на протяжении последних десятков материал — углепластик. Полимерные композиционные материалы на основе углеродных волокон обладают уникально высокой прочностью (в 1,5-2 раза выше прочности конструкционных сталей, а в некоторых случаях и до пяти раз, а плотность в 2-4 раза ниже) и легкостью, а также высокой устойчивостью к коррозии, возможностью избирательного оптимального армирования сложных форм деталей и другие преимущества. В космосе, где стоимость доставки груза сопоставима со стоимостью килограмма золота, углепластики стали активно применяться при создании новых машин. В восьмидесятые в СССР створки челнока «Буран» сделали из углепластика (челнок состоял на 13% из специальных пластиков), в девяностые использование композитных обтекателей позволило сократить вес ракеты «Протон» в полтора раза.
Где мы?
Если во времена фараонов композитные технологии были чем-то эксклюзивным, то сегодня углепластики все глубже проникают в самые разные аспекты нашей жизни. Например, менее десяти лет назад в воздух поднялся пассажирский самолет Boeing 787 Dreamliner, а в 2016 году — Airbus 350, они более чем наполовину состоят из композитов. В России скоро начнутся испытания нового пассажирского лайнера МС-21, на треть состоящего из композитов. Композитному или черному крылу можно придать в отличие от алюминиевого почти любую геометрическую форму. Это позволяет выпускать крыло с большим удлинением и лучшей геометрией, и при этом с меньшей массой и в конечном счете экономить 6-8% топлива. В боевой авиации композитные покрытия позволяют существенно снижать радиолокационную заметность самолетов. Мы обсуждаем возможность спроектировать и выпустить композитное крыло отечественного производства при создании нового широкофюзеляжного лайнера в сотрудничестве с нашими китайскими партнерами из корпорации Comac, полет намечен на следующее десятилетие. И экономия значительного количества топлива позволит существенно экономить выбросы углерода, что важно для экологии. Углепластик сегодня – неотъемлемый компонент строительства современных зданий и мостов, некоторых видов железнодорожных вагонов, его доля увеличивается при выпуске автомобилей.
По прогнозам компании Global Carbon Fiber Composites Supply Chain Competitiveness Analysis (подготовлен экспертами университета Tennessee и Oak Ridge National Laboratory), в ближайшие пять лет аэрокосмическая отрасль будет конкурировать с другими потребителями композитов. В 2018 году потребление композитов аэрокосмической индустрией оценивается в 13%, автомобильной промышленностью – в 20%, производстве всевозможных баллонов – от аквалангистов до цистерн — 22%, а ветряной энергетике – более 10% от общего объема потребляемых материалов.
Сегодня большую часть рынка занимают крупные международные конгломераты, штаб-квартиры большей части которых — в Японии или США. Наиболее крупный производитель композитов – японский химический конгломерат Toray. Оборот холдинга около $18 млрд, около 10% выручки приходится, собственно, на композиты. Композиты компания начала выпускать в начале семидесятых годов, после того как освоила выпуск нейлона, синтетических материалов и другой продукции. В пятерке лидеров – азиатские Mitsubishi, Toho, Formosa, эти компании специализируются в том числе на выпуске сырья – белой нити, из которой потом делают углеродное волокно. Среди крупнейших производителей ткани и препрегов – американские Hexcel и Cytec (последняя год назад вошла в европейский концерн Solvay с оборотом свыше 12 млрд евро). Есть в списке заметных потребителей и компании с экзотической историей. Например, австрийская FACC с оборотом более 1200 млн евро выросла из композитного направления европейского производителя спортинвентаря Fischer. По экспертным оценкам в настоящее время мировой рынок углекомпозитов оценивается свыше $3,1 млрд. с потенциалом удвоения каждые 5 лет.
Перспективы для «гаража»
Ежегодный объем мирового производства композитов сегодня оценивается в 65 000 тонн углепластика и около 2 млн. тонн стеклопластика. А к 2025 году прогнозируется рост потребления углеволокна в 2,5 раза — до 161 000 тонн.В последние несколько десятков лет пальму первенства взяли Япония, США и Китай. По уровню производства — свыше 7 кг композитных материалов в год, существенно опережают Россию (оценки потребления у нас – около 300 грамм на душу). Главные покупатели углепластика в России — авиация и космос, здесь стоимость производства килограмма изделия – около 1300 евро за килограмм. Но очень большой потенциал кроется в менее сложных сегментах, где килограмм стоит существенно меньше чем в авиации — €150 и €50. В таких сегментах, как автомобилестроение и транспорт, жилищно-коммунальный сектор, транспорт и производство спортивного инвентаря, сохраняют большой потенциал роста. Solvay оценивает рост рынка в аэрокосмосе не мене чем в 10% в год.
В России уже созданы заводы, технологиям которых могут позавидовать коллеги из других стран, например, завод «АэроКомпозит» в Ульяновске. крупные российские холдинги — «Роснано», Росатом — уже построили вполне современные мощности. Сегодня заводы в России выпускают около 1500 тонн углепластика, это около 2% мирового рынка, причем часть экспортируется. Ежегодное потребление авиацией – пока – около 25 тонн в год, перспективы применения в других отраслях помимо экспорта — огромны.
Одна из самых больших проблем использования композитов частным, в том числе, малым бизнесом и стартапами — высокая цена сертификации в России. ОАК построил один из крупнейших в мире заводов, где выпускается крыло для нового пассажирского лайнера МС-21 на безавтоклавной технологии, раньше никто по подобной технологии крупные агрегаты для самолета не делал. Много сделано в разработке отечественных смол и материалов, в том числе, Всероссийским институтом авиационных материалов (ВИАМ). Лишь немногие корпорации — Boeing, Airbus или «Сухой» — могут тратить годы дорогостоящих исследований, продувок в аэродинамических трубах или работы на суперкомпьютерах — для квалификации и сертификации к применению композитных агрегатов в самолетах.
У нас есть масса возможностей использования материалов с лучшими по сравнению с традиционными свойствами. Самый простой сегмент — жилищно-коммунальное хозяйство. В большинстве стран мира строители давно используют стеклопластиковые трубы для мусоропроводов. Стеклопластик эластичен, может растягиваться, он обладает отличными антибактериальными свойствами, легче бетона. Есть некоторые оценки, по которым цена углепластика для производства спортивного инвентаря — удочек, хоккейных клюшек и пр — не более €50 за килограмм.
Уже сейчас очевидно, что со временем композиты будут вытеснять металлы, как например, это уже происходит в строительстве и судостроении (карбоновый корпус корабля практически незаметен для радаров, чем металлический). Огромные ожидания связаны с ветроэнергетикой. Несколько крупных российских и иностранных компаний объявили о планах установки полей ветрогенерации. А лопасть современного ветряка почти в два раза длиннее крыла пассажирского самолета. Сегодня в России и мире проводятся эксперименты с созданием сложных конструкций. Вплетение (внедрение) в структуру конструкцию оптоволокна позволяет в режиме реального времени определять ресурс, например, крыла самолета – лазер улавливает микроповреждения конструкции, если она столкнется с птицей или получит повреждения от нерадивых техников на земле. Со временем комбинации будут сложнее. Так что поводов следить за новинками в отрасли и удивляться – впереди еще множество.