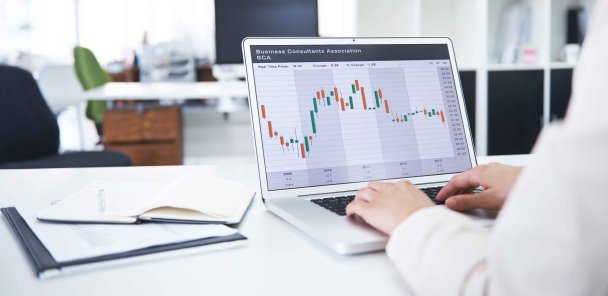
Возможности прогнозных моделей только начали исследовать. В будущем, возможно, они станут применяться для решения сложных социальных задач — по регулированию международных отношений, для настройки глобальной финансовой системы, борьбы с оборотом наркотиков. Глава SoftBank Масаёси Сан уверен, что искусственный интеллект может стать той технологией, которая поможет избежать угроз существованию всего человечества, среди которых пандемии, вооруженные конфликты, падение метеорита и прочие. Пока это звучит как фантастика, но на практике прогнозные модели уже могут приносить пользу в отдельных компаниях и на промышленных предприятиях. Они помогают улучшить качество выпускаемой продукции, усовершенствовать процесс производства, помочь технологам сократить затраты времени и сырья.
Так, например, в компании Северсталь прогнозные модели используют для анализа работы оборудования, которое производит слябы. Слябы — куски металла, которые получаются, когда расплавленное сырье льют в форму, остужают, а потом рубят и остужают. Эти заготовки потом снова разогреют и сделают из них металлопрокат, трубы или даже фольгу. Сляб — промежуточное состояние стали перед тем, как ее превратят в конечный продукт. Важно, чтобы в заготовках не было трещин, иначе слиток может разрушиться при последующей прокатке. Иногда такие дефекты можно устранить, если они на поверхности, но в некоторых случаях трещины оказываются внутри, и заметить их невозможно. Кроме трещин у слябов может быть множество других недостатков: пузыри, смещения, наросты и прочие. За качеством заготовок следит специальная лаборатория на заводе. Выявление дефектов — это целая наука. Каждый слиток остужают, перемещают с машины, снимают верхний слой, осматривают со всех сторон, анализируют с помощью ультразвука, рентгеновского аппарата, лазерных сканеров и прочего сложного оборудования. Каждый сляб проверяют на триста параметров, эта процедура занимает несколько часов и стоит очень дорого.
После проверки определяется дальнейшая судьба заготовки — можно ли из нее сделать трубу, металлоконструкцию для нового здания, мелкие стальные изделия или что-то другое. Через лабораторию проходит четверть всех выпускаемых на заводе слябов. Но туда поступают не случайные заготовки, а совершенно конкретные. На предприятии много лет использовалась специально разработанная математическая модель именно для определения того, какие слябы нужно проверить. Этот подход позволял выявить 9-10% дефектных слитков, которые есть в среднем в каждой партии. За два года через такую лабораторию на Северстали прошло двадцать тысяч слябов — это колоссальные затраты времени и денег.
Быстрое качество
Технологии анализа больших данных позволили Северстали сократить время на проверку слитков на четверть, число проверок уменьшить на 80%, при том, что теперь точность выявления дефектов равна 95%. Пилотный проект занял всего три месяца. Над ним работали четыре специалиста SAP и технические эксперты предприятия заказчика. Для построения прогнозной модели снимались показания с установки непрерывного разлива стали: данные новой плавки, информация о процессе разливки с датчиков. Анализировались параметры проверки слябов и данные ОТК — службы, которая готовит список слябов для отправки в тестовую лабораторию. Когда модель была готова — на ее создание понадобилось всего две недели — группа проекта предоставила новый созданный список. Предприятие полтора месяца проверяло новую методику. В итоге стало ясно, что система SAP HANA построила более совершенную модель, которая учитывает влияние двадцати различных показателей процесса выплавки слябов (температура и давление воды на разных этапах, скорость разливки плавки, вибрация и другие показатели) на возникающие дефекты. Оказалось, что специалисты, которые работали со сталью десятки лет, многие параметры даже не отслеживали, просто потому что работа машины описывается десятками тысяч характеристик и сложно «вручную» за всеми уследить, выявить корреляции. Финансовый расчет показал, что проект внедрения этого решения окупится в Северстали всего за 14 месяцев.
Чистый лист
Алгоритмы прогнозирования событий используются в широком спектре задач. Мы уже приводили пример того, как система предсказания ремонтов помогает итальянской железнодорожной компании экономить миллионы. На бумажном комбинате близ города Грац в Австрии большие данные помогают избегать разрывов бумажного полотна на производственных станках.
На заводе работают бумагоделательные машины, конструкция которых внешне напоминает танк, в котором вместо колес — рулоны готового полотна. Такая установка работает непрерывно, выпуская бумагу и картон со скоростью 1400 метров в минуту. Один из важнейших этапов производства — сушка полотна. В этой части машины наиболее вероятны разрывы. За год это может происходить в среднем 400 раз. Если случается разрыв полотна, то вся линия останавливается и требуется вмешательство ремонтников. На устранение обрыва может уходить от 30 минут до нескольких часов. Иногда в результате в брак попадает часть партии готового продукта. Если успеть спрогнозировать разрыв хотя бы за десять минут, то работник может замедлить линию, а бригада инженеров — устранить проблему до того, как она возникнет, и снова запустить машину на полную скорость. Именно для этого с некоторых пор предприятие использует SAP HANA. В систему загрузили данные с датчиков бумагоделательной машины, собранные за год работы. Через неделю была готова прогнозная модель, которую предприятие сразу же начало использовать. В итоге количество разрывов сократилось в два раза.
Еще одно предприятие по производству бумаги, расположенное на севере Германии, использует прогнозные модели для других целей. На заводе выпускается несколько типов продукции, причем смена происходит несколько раз в неделю. Каждый раз требуется перенастройка машины, которая производится вручную — технологи примерно знают, что нужно подкрутить, чтобы производилась бумага нужного типа. На то, чтобы добиться необходимого качества после перенастройки, требуется запустить машину несколько раз — произвести 4-5 итераций. На каждую такую итерацию требуется примерно полчаса: 15 минут на настройку, 15 минут на прогон. Во время тестовых запусков тратится сырье. Специалисты SAP установили на машину сотню датчиков и собирали данные с них в течение трех месяцев. Затем для каждого типа продукции была построена модель, которая давала рекомендательные настройки. Благодаря этому число тестовых итераций сократилось до одной, на 80% сократилось время перенастройки и удалось сохранить существенное количество сырья.