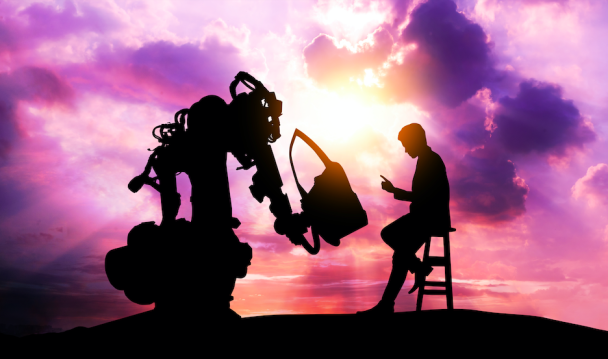
Пятая промышленная революция может случиться, когда цифровые решения, внедряемые сейчас как пилотные проекты, станут для предприятий реальностью. По прогнозу экспертов McKinsey, в 2025 году вклад индустриальных цифровых технологий в цепочки создания стоимости для производителей и поставщиков превысит $3,7 трлн, что как раз и может привести к качественному прорыву в индустрии. Новейшие технологии уже активно внедряются на производстве — по данным PwC за 2019 год, 71% производителей США создают или тестируют решения, связанные с индустриальным интернетом вещей (IIoT). Большая часть из них (60%) используют IIoT в проектах внутри своих компаний, 57% — при работе с партнерами, контрагентами и в цепочках поставок, а 58% — при работе со своими B2B-клиентами.
«Cегодня организациям приходится работать в условиях стремительных изменений. Без использования современных технологий бизнесу очень трудно обеспечить необходимый уровень гибкости, чтобы к ним адаптироваться. Технологии стали ключевым инструментом в «перезагрузке» предприятий, способствуя развитию инноваций даже в традиционных областях, таких как промышленность, — отмечает Кристина Тихонова, президент Microsoft в России. — Компании осознают, что технологии позволяют не только эффективно организовать бизнес-процессы и взаимодействие между сотрудниками на крупных предприятиях, но и обеспечить соответствие требованиям производственной безопасности, исключить человека из рутинных и опасных производственных процессов, снизить стоимость обслуживания оборудования и многое другое».
Сценарии применения инноваций могут быть совершенно разными. Например, когнитивные сервисы могут использоваться для решения отдельных производственных и организационных задач, таких как анализ изображений для контроля регламентных процедур, а технология цифровых двойников — для комплексной оптимизации производственно-сбытовой цепочки, включая выявление возможных сбоев еще до начала эксплуатации. Кроме того, технологии предиктивной аналитики и предиктивного обслуживания (predictive maintenance) в сочетании с элементами сети IIoT эффективно применяются для планирования обслуживания капитальных активов, оптимизации режимов работы оборудования и т. д.
Подробнее о том, как цифровизация меняет промышленность и каких эффектов с ее помощью добиваются предприятия, — в нашем слайд-шоу.
* На правах рекламы
Индустрия 4.0 сильно изменила сам подход к восприятию производственных процессов. «Технологии являются ключевым инструментом трансформации бизнеса, и интернет вещей не исключение», — отмечает Кинга Пикуч, директор по индустриальным решениям для корпоративного сектора Microsoft в Центральной и Восточной Европе. Датчики и иные устройства в режиме реального времени мониторят как ход процессов, так и состояние оборудования. По данным PwC, 44% производителей уже используют интернет вещей в прогнозном техническом обслуживании, еще 27% планируют сделать это в течение двух лет.
Развитие промышленного интернета вещей позволяет расширить взгляд на производство. «За счет доступной и понятной информации оператор получает ясное представление обо всех условиях протекания процесса, на основе которой могут приниматься более качественные решения, что делает работу предприятия более безопасной и предсказуемой», — говорит Андрей Ванюков, руководитель отдела продаж решений Emerson. «Цифровизация дает жизненно важные в условиях конкурентной борьбы преимущества: например, повышает эффективность работы за счет той информации, которую ранее невозможно было получить вообще или только после больших вложений. Изначально беспроводные решения были ориентированы на единичные удаленные объекты, находящиеся в стороне от основных производств, но сейчас они нашли применение практически во всех отраслях», — добавляет Денис Тагиров, управляющий по развитию бизнеса средств измерений в СНГ Emerson Automation Solutions.
По данным Emerson, онлайн-мониторинг может помочь сократить время незапланированного простоя оборудования на 43%, количество опасных инцидентов на заводе на 50% и сэкономить до 50% при ремонте оборудования за счет обнаружения проблемы до поломки.
Еще один немаловажный эффект, особенно в быстро меняющихся условиях, — экономия времени. По данным компании Honeywell, еще одного ведущего поставщика решений, позволяющих предприятию объединять данные от разных устройств разных производителей на одной платформе, интернет вещей дает возможность компаниям быстрее реализовывать проекты: время выпуска проектной документации сокращается на три-четыре месяца, а трудовые затраты по инжинирингу — на 20%. В одном конкретном проекте Honeywell удалось сократить незапланированные простои на 90%.
Дионисиос Ставракас, директор по продажам корпоративных решений Honeywell, отмечает, что многие производители даже не знают, что происходит на их предприятии, потому что выяснять это слишком дорого и долго. До недавнего времени промышленники избегали инвестирования в IIoT, так как полагали, что это лишь более простой способ просмотра данных, которые они уже получают. «Конечно, IIoT выходит далеко за рамки простого сбора данных. Главная ценность — понимание и рекомендации, как улучшить процессы в компании, которые поступают в режиме реального времени», — подчеркивает Дионисиос Ставракас.
Эксперт выделяет три основных преимущества внедрения IIoT: повышение производительности, поддержание устойчивого развития компании и безопасности сотрудников. «Наше программное обеспечение для управления предприятиями Honeywell Forge помогает клиентам с помощью облачных вычислений, технической связанности всех объектов и искусственного интеллекта агрегировать разрозненные операционные данные и получить инсайты, необходимые для принятия практических решений. Это позволяет достичь более высокой производительности», — говорит Дионисиос Ставракас.
Он также добавляет, что цифровые решения активно внедрялись в топливно-энергетическом комплексе и в авиации. Например, облачная аналитика программного обеспечения Honeywell Forge позволяет оптимизировать эксплуатацию и маршрутизацию воздушных судов, что приводит к измеримой экономии топлива в каждом полете.
Наиболее активно решения промышленного интернета вещей внедряются в нефтегазовых компаниях, энергетике, металлургии. Один из ярких кейсов Emerson — проект автоматизации добычи и поддержания пластового давления нефтегазового месторождения в Казахстане на базе IIoT PlantWeb. На трубопроводе не было контроля за пластовым давлением, в результате его разрывы определялись несвоевременно. Это приводило к существенным денежным потерям в виде недозакачки воды в нагнетательные скважины и, как следствие, недополученной прибыли за нефть, а также повышенным расходам на водоснабжение. С внедрением беспроводных технологий мониторинга предприятию удалось повысить безопасность, улучшить и облегчить условия работы обслуживающего персонала, повысить дебит скважин, сократив при этом затраты на обслуживание скважин на 65%.
А в рамках проекта Emerson в Поволжье нужно было оперативно автоматизировать контроль уровня нефтепродуктов и давления в резервуарах хранения. Внедрение беспроводных технологий PlantWeb позволило сократить затраты на автоматизацию на 34% и оперативно устранить предписания контролирующих органов: время пуска сократилось в шесть раз, притом что качество монтажа выросло.
Впрочем, производственные предприятия других сфер тоже уже оценили эффект от цифровизации. Кармело Чинарди, вице-президент компании PTC, вспоминает кейс европейского производителя упаковки для пищевых продуктов. Только благодаря цифровой системе мониторинга состояния активов и производственных KPI предприятию удалось сэкономить более $20 млн.
Еще один стимул к внедрению решений, позволяющих принимать решения на базе мониторинга производственных процессов и работы оборудования в режиме реального времени, — растущее внимание к вопросам устойчивого развития и эффективности использования ресурсов. Как отмечает Дионисиос Ставракас из Honeywell, облачная платформа, объединяющая данные систем отопления, вентиляции и кондиционирования воздуха, помогает владельцам зданий лучше контролировать расходы и сокращать углеродный след.
Сейчас все крупные промышленные компании понимают, что больший эффект дают комплексные, интегрированные решения — в рамках отдельно производственной площадки или всего предприятия. «Мы наблюдаем экспоненциальный рост всех наших решений для цифровой трансформации, — говорит Кармело Чинарди, вице-президент PTC. — Такие интегрированные решения могут помочь компаниям снизить затраты и риски при одновременном повышении эффективности и результативности, не говоря уже о том, что они могут поддерживать значительные стратегические сдвиги, включая изменения в бизнес-моделях».
Повышенный интерес компаний обусловлен в первую очередь высокими ожиданиями эффектов и выгод, подтверждает Никита Атамасов, старший консультант практики платформенных решений SAS Россия и СНГ. «Компании дозрели до масштабных цифровых проектов с точки зрения количества данных и зрелости базовой автоматизации. При этом для новых отраслей и эффект будет заметнее и значительнее, чем для тех компаний, которые уже прошли значимую часть цифрового пути», — отмечает Атамасов.
По словам Кармело Чинарди, внедрение решения платформы IIoT позволяет компаниям быть более гибкими, эффективными и действенными: «Фактически, имея возможность получать данные в реальном времени из цеха и контролировать пропускную способность, общую эффективность оборудования и другие аспекты, компании могут повысить операционную эффективность и снизить бизнес-риски — как традиционные, так и вытекающие из новой нормы. Интегрированные решения обеспечивают производителю гибкость, которая позволяет улучшить качество обслуживания и удовлетворенность клиентов».
Важная сфера применения комплексных цифровых решений в промышленности — безопасность труда. По данным PwC, 39% производителей улучшили безопасность предприятия с помощью интернета вещей, а 44% планируют сделать это в течение следующих двух лет. Использование технологий — биометрии, распознавания изображений и датчиков окружающей среды — позволяет производителям лучше контролировать физический доступ и безопасность активов и систем, а также безопасность работы в цеху. Подобный контроль можно осуществлять на всех частях производства — например, для горно-обогатительного комбината это может быть территория цеха, карьера и проведение погрузочно-разгрузочных работ.
Во время пандемии COVID-19 задач, решаемых с помощью систем видеоаналитики, прибавилось. Теперь предприятия с их помощью ищут тех, кто не соблюдает социальную дистанцию, снимает маски или идет на слишком длительный контакт с коллегами. Система сама выявляет нарушения на видео, высылает уведомления ответственному лицу (в формате онлайн-отчетности, sms, e-mail — как удобно), ведет список нарушителей и даже предлагает уточнить правила, если видит существенные проблемы в их исполнении. Тренд на компьютерное зрение был заметен задолго до пандемии, но сейчас спрос растет, отмечает Андрей Матвеенко, старший консультант SAS.
Промышленный интернет вещей играет ключевую роль в создании экосистемы вокруг компании: цепочки поставок одного предприятия становятся связанными с цепочками поставок другого предприятия, одно производство обменивается информацией с другим. Решения IIoT могут отслеживать состояние продуктов с момента добычи сырья для их изготовления до прибытия в конечный пункт назначения. Системы с использованием машинного обучения помогают оптимизировать маршруты доставки, уменьшить количество ошибок и свести к минимуму мошенничество. По данным PwC, из промышленных производителей 41% уже почувствовал на себе преимущества внедрения интернета вещей в цепочках поставок, а еще 40% надеются увидеть эффект в течение двух лет.
Во время пандемии организации столкнулись с нехваткой сырья и задержками поставок, что привело к увеличению времени производства и расходов компании. Интернет вещей стал одной из тех технологий, которые помогали свести эти проблемы к минимуму. Например, решение Luminate Control Tower от Blue Yonder отображает распространение COVID-19 и связанное с этим принятие ограничений в разных регионах, чтобы при сопоставлении с данными по цепочке поставок фирмы идентифицировать возможные узкие места. Это решение, основанное на облаке Microsoft Azure, а также на системах прогнозирования на основе искусственного интеллекта и машинного обучения, использует данные из всей цифровой экосистемы, что позволяет ей уменьшать расходы до 30% и повысить эффективность планирования на 60%.
Цифровой близнец — это точная виртуальная копия физических объектов, объединяющая данные со всего производственного цикла и из различных экосистем поставщиков, контрагентов и организаций. «От эффективного использования цифровых близнецов и возможности делиться актуальной информацией получают выгоду все — и компания, и ее сотрудники, и контрагенты, — говорит Анна-Мария Уолтерс, директор по глобальному маркетингу Bentley Systems. — Инженеры тратят меньше времени на поиск и проверку информации и могут уделять внимание оценке различных вариантов и поиску лучших решений. Обслуживающий персонал получает доступ к точной информации о работе предприятия и может быстро принимать решения, избегая простоев. Владельцы заводов получают более безопасный и производительный завод, а поставщики оборудования и подрядчики могут предоставлять больше услуг с добавленной стоимостью».
Bentley Systems совместно с Schneider Electric создала цифровую копию новой шестиэтажной штаб-квартиры Microsoft Asia Pacific в Сингапуре: менеджеры объектов используют цифровую копию для мониторинга потребления энергии, качества воздуха, заполняемости помещений и температуры во всем офисе и т. д. Есть и более масштабные проекты — например, цифровые копии участков железнодорожных сетей в Великобритании и Италии. Благодаря использованию цифровых близнецов для интегрирования конструкторских решений с информацией по эксплуатации, металлургический завод в китайском Лаотине уменьшил потребление энергии некоторых цехов завода на 70%, а производитель цемента в Фуцзянь, по расчетам, сократил эксплуатационные расходы на 30%.
Создать единую экосистему интернета вещей можно и внутри одного вертикально интегрированного холдинга, объединив данные с разных предприятий. Подобное решение Bentley Systems предложила для «Волгограднефтепроекта». Его заказчик работал над возведением семи платформ, введенных в эксплуатацию в Каспийском море. На «Волгограднефтепроект» была возложена задача наладить процесс управления инженерной и технической информацией от разных подрядчиков на этапе проектирования, чтобы создать консолидированную 3D-модель для использования во время строительства. Сам «Волгограднефтепроект» отвечал за техническое проектирование платформы блок-кондуктора и теперь занимается задачами по его модификации.
«Волгограднефтепроект» также отвечает за создание 3D-модели объектов и за связанную с ней техническую информацию, используемую во время эксплуатации. Для этого он использует платформу Bentley AssetWise, которая помогает собирать данные из множества различных систем в единую информационную структуру. В результате проектная группа построила информационно насыщенную цифровую модель инфраструктуры нефтегазового месторождения, которая соответствовала уже построенным объектам. Решение обеспечивало точную поддержку принятия решений для инженерных, строительных, эксплуатационных и ремонтных бригад. Благодаря созданию единой экосистемы время поиска данных сократилось на 30%, время обмена ими между платформами — на 70%. Благодаря использованию цифровой модели компания рассчитывает снизить ежегодные эксплуатационные расходы месторождения минимум на 30%.
Доказывать пользу цифровизации, казалось бы, уже не нужно. Но тем не менее многие промышленники не спешат внедрять новые технологии.
По мнению экспертов SAS, многих из них останавливает сложность в расчете экономического эффекта по некоторым направлениям. Например, если поставлена цель повысить качество произведенного товара, то можно явно оценить процент брака и степень роста доли высокосортной продукции. Но если цель — предотвратить нештатные ситуации с оборудованием, то при расчете экономического эффекта будет сложно учесть все возможные финансовые потери от аварии. Для преодоления этого барьера эксперты советуют начинать цифровизацию с тех частей производств, где может быть достигнут максимальный ощутимый эффект.
Действительно, процесс цифровой трансформации не так прост, и бизнес может теряться, не знать, с чего начать, подтверждает представитель Honeywell. Но уже сейчас рынок предлагает облачные решения и программное обеспечение, которое способно централизовать данные и обеспечить единую точку интеграции вне зависимости от того, какие платформы заказчик использовал ранее.
Кинга Пикуч из Microsoft отмечает среди сдерживающих факторов сложность внедрения и нехватку ресурсов. Чаще всего клиентский опыт в сфере IoT состоит из трех этапов, каждый из которых предполагает конкретные бизнес-результаты и эффект от инвестиций, начиная со снижения затрат и заканчивая повышением качества обслуживания клиентов, рассказывает Кинга. Во-первых, это проведение проверки концепции для четкого определения бизнес-потребностей. Во-вторых, подготовка к масштабированию (синхронизация между отдельными бизнес-единицами). В-третьих, масштабирование на всю организацию.
С чего компании начать при внедрении цифровых решений? С сессии по разработке идей для бизнес-сценариев, в которой примут участие как менеджеры, так и специалисты технической части, советует Пикуч.
Прежде чем двигаться дальше, компания должна понять свой текущий уровень зрелости по отношению к организациям с успешным внедрением IoT, обычно оценивая себя по трем показателям: человеческий ресурс, технологии и бизнес. «Далее начните реализацию выбранного сценария, собирая информацию о физических объектах, подключив их к облаку для повышения эксплуатационной эффективности. Выберите облачную платформу, такую как, к примеру, Microsoft Azure IoT, способную подключать любые устройства интернета вещей, поддерживающую несколько решений и позволяющую быстро их масштабировать, — советует Пикуч. — Анализируйте и визуализируйте данные физических объектов с помощью предиктивной аналитики и машинного обучения для выявления закономерностей, основанных на исторических данных и данных, близких к реальному времени. Определите принципы для построения стратегии работы с данными предприятия. А после сосредоточьте внимание на интеграции в существующие бизнес-процессы и создании устойчивой долгосрочной инфраструктуры для использования IoT во всей организации».
«Все необходимые ресурсы и услуги сегодня доступны по клику, но важно помнить, что они также доступны и для ваших конкурентов, — предупреждает Кинга Пикуч. — Ваша задача — быть первым, оставить позади других».